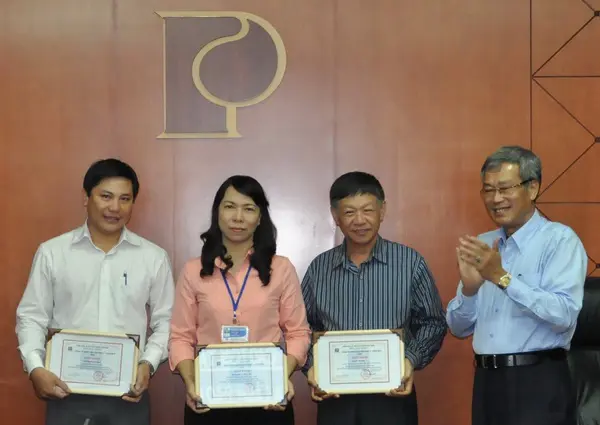
Ho Chi Minh City, December 18th 2013, Petrolimex Saigon held to review the integrated management system of quality – safety – health and environment (QSHE) according to the requirements of ISO 9001:2008, ISO 14001:2004 and OHSAS 18001:2007 standards, at planned intervals. Also on this occasion, the company awarded PSG Prizes in 2013 to commend three outstanding individuals of quality (P – Productive Prize), Safe (S – Safe Prize) and environment (G – Green Prize).
-Productive Prize: Nguyen Van Ngoc – Manager of Station No.13
-Safe Prize: Vu Van Diet – Specialist of Technical Safety and Environment Department
-Green Prize: Nguyen Thi Bich Lien – Specialist of Administration Department
Chairman of Quality Board, Deputy Director Nguyen Van Canh
awarding PSG Prizes for outstanding individuals
The meeting summarized the main activities in order to generalize the quality works which have been taking place in 2013 with the following points:
![]() |
1)For certification maintenance activities: In2013,Bureau Veritas Certification (BVC) conducted to audit the re-certification and surveillancefor QSHE management system according to the periodical. The companyimplemented the needed corrective action and finished on time in order to ensure that the certificateshave been effected continuously.
2)For quality management activities: the company had the following typical activities:
-Key performance indicators (KPI) have been combined with the company’s objectives. They have become the important indicators to evaluate the work efficiency and the results of business activities.
-Documentation has been improved continuously in form and content. The new documentsare issued to ensure the quality of work which are done according to the principle of 5W – 1H (Who?, What?, Where?, Why?, When? and How?).External documentation has been updated, sorted by fields and posted on STM software to help users in readily identifiable; and weekly, the legal newsletters are sent to staffs and employees by mail exchange.
-Beside internal audit activities have been heldat planned intervals, units self-organized to audit once a year in oder to contribute to enhancethe sense of initiative of units in self-assessment activities.
-Management review has been maintained regularly twice a year to ensure that the system has been operated continuously and effectively.
-Focus on internal training programs as seminars on quality for ISO experts at departments/divisions, 5S methodology for staffsand employees of Headquarter Office, Nha Be Oil Terminal,Central Laboratory, ... In addition to internal training programs, the company also organizedthe advanced internal audit course for IQA Team as Bureau Veritas Certificationtrained to enhance the knowledge and skills of assessment for this core team.
-The 5S Newslettershave regularly maintained every month on the internal websiteof company and units in order to propagate and create the emulation movement between departments and units.
After more than 10 years of applying the management system according to the standards, Petrolimex Saigon not only has met the requirements of the standards but also has improvedcontinuously the quality management system through the application of innovative tools such as 5S practice program, risk management, ... On that basis, orienting thequality managementof 2014 as follows:
-Continue to restructure documentation, business processes in order to ensure the compatibility between the documentsand the applicable program (eGAS, ERP, STM, maintenance equipments, etc.).
-Continue to maintain the 5S practice programin the whole company, units and retail petroleum stations through the monthly audits and the 5S Newsletters in order to contribute to build the image of Petrolimex Saigon “Green–Clean– Beautiful – Safe”.
-Implement risk management program for the prevention of potential risks and increase readiness of response for possible risks which can affect the business activities of the company; at the same time,combineKey Risk Indicators (KRI) with Key Performance indicators (KPI) to become measurement indicators regularly.
-Improve continuously the service quality with the efficiency control tools and customer care activities regularly, such as holding a customer conference, conducting customer satisfaction surveys, answering the adequacy of the questions/recommendations from clients, ...
-Continue the program of re-training for ISO experts at departments/divisions and expand the training of quality general knowledge for new and potential quality team.
-Maintain the regular activities (control of documents, the measurement of process capability, internal audit,external audit and verification of corrective – preventive action, ...) in an efficient manner.
The above orientation will become“guideline” in quality activities in 2014, performing commitment of Petrolimex Saigon leaders for the implementation, maintenance and continuous improvement of QSHE integrated management systemto continuously improve service quality, to meet the increasing demands from customers.
Some pictures of maintenance and improvement activities of quality management system in 2013:
Deputy Director Nguyen Van Canh opening the internal auditor and the skills of 5S pracetice course
![]() | ![]() |
Quality Manager Dao Van Hung | General view of 5S practice course |
![]() | ![]() |
Quality Manager Dao Van Hung training quality management for ISO experts at departments / divisions | Quality Manager Dao Van Hung guiding to compose the business processes |
![]() | ![]() |
Records, papers are set in order to cabinets and shelve | Motorcycle Parking |
![]() | ![]() |
Place to hanging personal protective clothing | The fire store |